Innovation, productivity, and compliance
In process and chemical manufacturing, digital technology picks up when your sophisticated production equipment and control devices reach their limits. The right process and chemical manufacturing software makes it easier to meet customer needs with an optimal balance of flexibility and efficiency, creating the formulas you want to test and produce within a solid compliance framework.
Enablement at any stage of your process manufacturing business
Increase production throughput, cut production delays, do away with costly errors and inefficiencies, and boost the performance of your assets. Sikich process manufacturing teams put to work our extensive industry expertise together with our ERP and CRM software capabilities to connect and automate processes and data flows throughout your operation and supply-chain relationships.
As one of the top three NetSuite partners in the world, and 2022 North America Partner of the Year, Sikich assists you in implementing and fine-tuning NetSuite to manage and grow your business and its customer relationships. We collaborate with you to implement, configure, integrate, and run your process manufacturing software environment, and make sure it truly meets your company’s specific business goals.
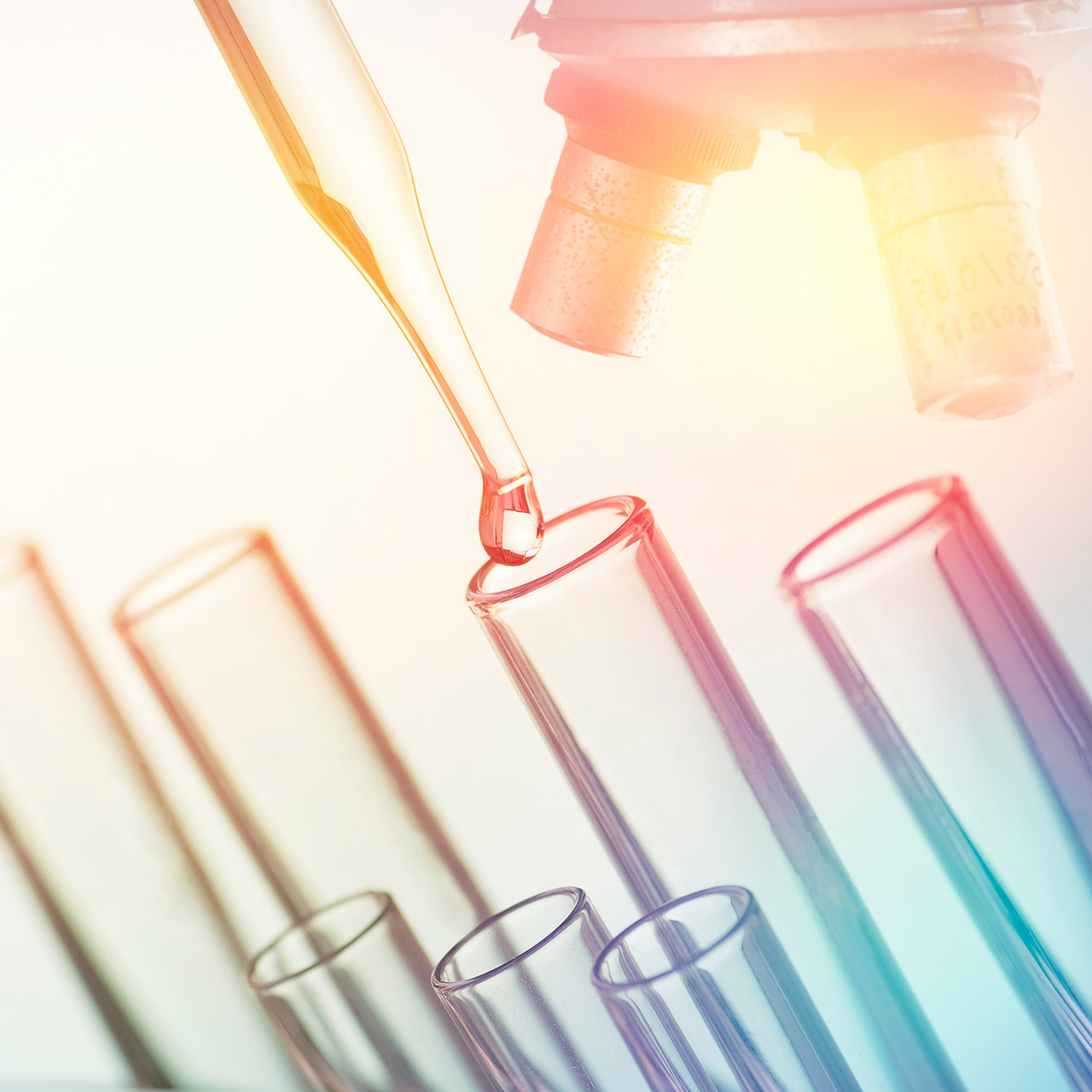
Creating real business outcomes from your processes and innovations
Improve accuracy, optimization, and control with NetSuite software, configured for chemical and process manufacturing to drive operational excellence and grow revenue.
Whether you process basic chemicals, specialty chemicals, pharmaceuticals, agricultural products, or consumer goods, Sikich’s team of experts can help you improve your efficiency and productivity, gain greater agility, or ready your company for strategic business transformation.
Formula Design
Optimizing design based on elements such as cost, potency, or density is key. The system’s efficacy is further enhanced by refining values and running multiple “what-if” scenarios, providing invaluable real-time feedback.
Recipe Management
The ability to effortlessly create and maintain multiple formulas or recipes streamlines operations, alongside establishing the yield of components. Security features are enabled to restrict access; only designated users can view, modify, and approve formulas.
Inventory Management
Tighter controls pave the way towards a more reliable inventory, which you can easily manage using a robust, multi-site warehousing system.
Batch Manufacturing
Combining multiple orders into a single batch streamlines operations, while approved users are empowered to make on-the-fly substitutions for greater production flexibility. The process is augmented with the capability to easily trace lots from raw materials all the way to finished goods, providing deeper quality control at both the product and lot level.
Quality Control
The system allows for flexible quality control, accommodating a variety of batch steps or incoming materials, ensuring thorough inspection and compliance at every stage. Certificates of Analysis (CoA) can be quickly generated from either a batch record or sales order, streamlining documentation and verification processes.
Compliance
By utilizing lot trace recall to track items throughout their lifecycle—from purchase, through production, to sales orders—administration time is significantly reduced. The system streamlines the completion of regulatory and global HAZMAT documentation, allowing for the management of multiple jurisdictions within a single order at the click of a button.