Dynamics 365 Work Policies are a Warehouse Management functionality in Dynamics 365 for Finance and Operations (D365FO) you can apply to any location but are only useful in specific scenarios and with certain situations. As you will see, you should only specify these policies on Production input or output locations that will help you to prevent work from being created when it’s not desirable. These policies can also be beneficial in directing material from the production lines directly to outbound trailers or locations for the shipping of transfer orders.
Creating New Dynamics 365 Work Policies
When you initially open the form and create a new Work Policy, the first thing you must do is name the Policy. For my example, I’m not going to put much thought into the name, but in a real-world solution, care should be used in naming the Policy so that it can accurately describe the function it is intended to perform. Naming values is often overlooked since it is not typically set up on a daily basis, so you may not notice the Policy or need to use it again for a while. Therefore the name of the Policy needs to remind you and others of what the function is doing.
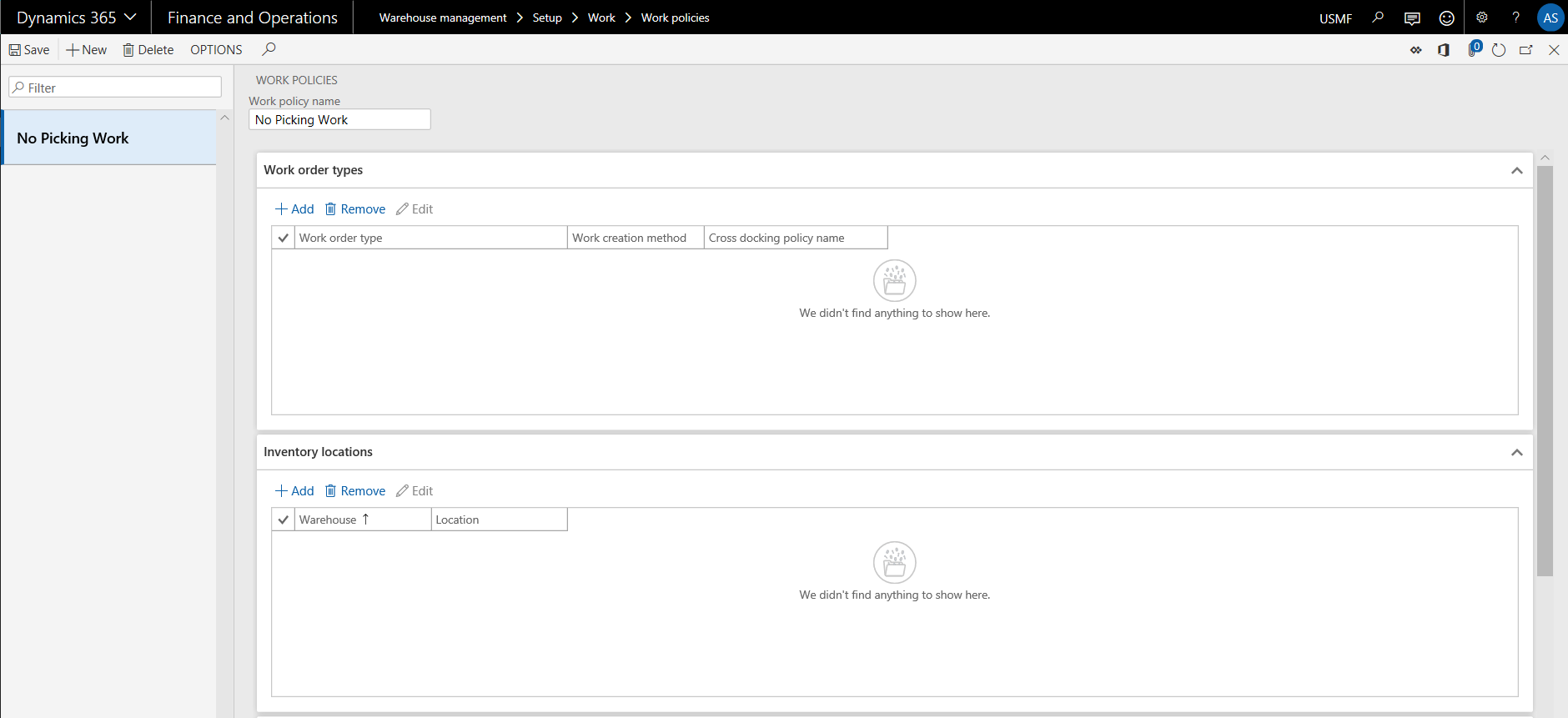
For the first example, I’m using the name of “No Picking Work” to describe the function for which I intend this to be used.
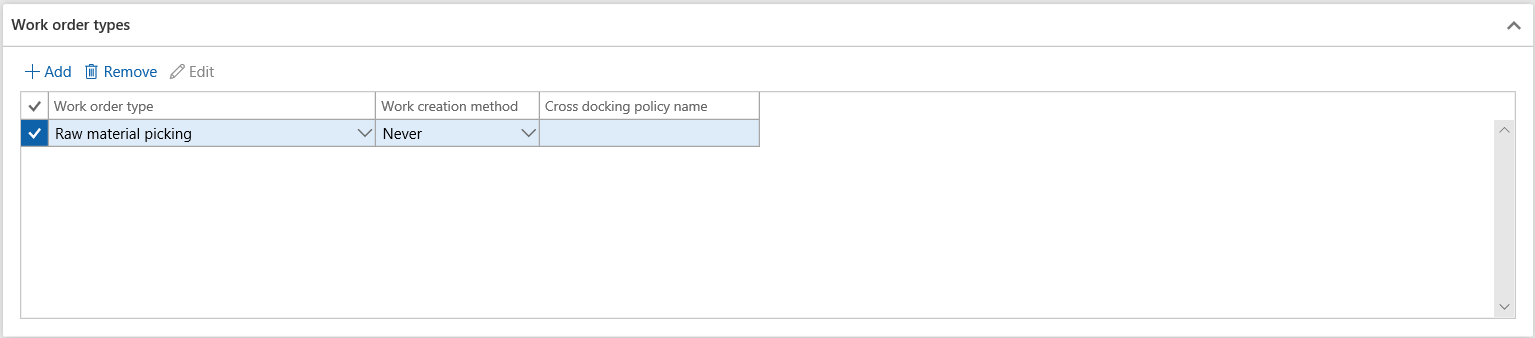
Next, you will assign the Work Order Type that will apply to the setup of the Policy. I’m going to use the value of “Raw Material Picking” in this example.
However, not all values can be used from the drop-down. The list shows all possible Work order types, but only the following are available for Work Policy functionality.
- Raw material picking
- Finished goods put away
- Co-product and by-product put away
If any other value is selected, an error will appear and not let you proceed with the setup. But you can add more than one of these values on your Policy and can use the same value to control all your locations.
The value for the field Work Creation Method will default to a value of “Never” and is the value that will be used in this example.
There is only one other possible value called “Cross-docking,” and this value will allow the user to create the process where inventory is moved directly to an outbound location for shipping against a transfer order, but we’ll cover the entire cross-docking set up another time.
The value of “Never” is what allows the user to override whether these work types are created or not.
There is one point of clarification that needs to be made regarding this functionality. When using a Work Order Type of “Raw Material Picking,” you are not stating that picking work should not be performed for a specified location. If you want to tell D365FO never to create picking work from a certain location, no matter where it is going, that is not how this works. This function will only limit any picking work from being created when work is to be picked to this location. So, when using Raw Material Picking types, it is only of benefit when set on Production Input locations to prevent picking work from being performed to that location.
For “Finished Goods Put Away” and “Co-product and By-product Put Away,” this works to control whether work is created on the Production Output locations.
Selecting Locations for the Policies
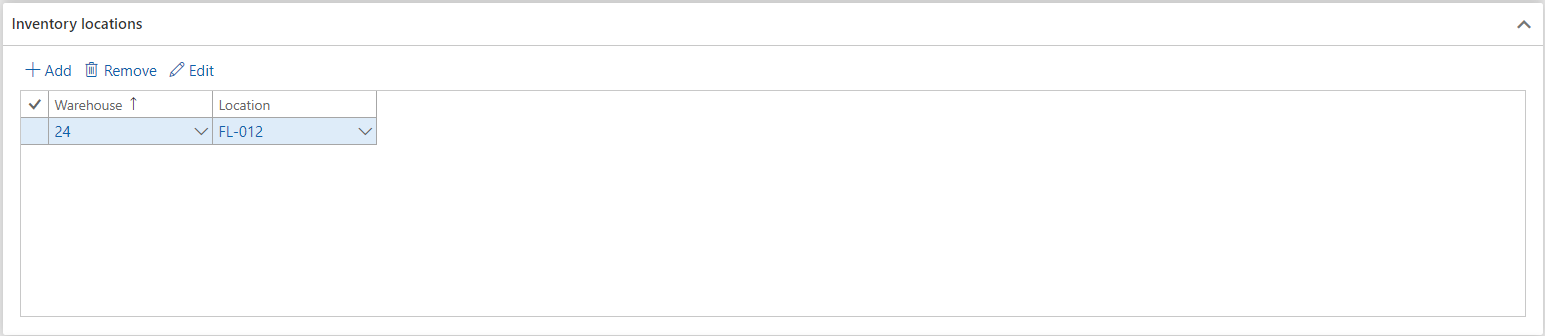
In the section for Inventory Locations, you can specify the locations to which this policy should apply. For this example, we will limit the location “FL-012” not to create any picking work when it is the production input location.

Alternatively, the Work Policy can be assigned to locations via the Locations form in the field shown above. Both setups accomplish the same result.
The locations specified should be either the applicable Production Input or Production Output locations, as this is where the values would have the intended effect, and setting the values on other types of locations will not produce the desired result.
A good point of usefulness for this setting is that if you apply it to a Production Output location, you can now use that location as the Default Production Output location in the setup of the Warehouse, even if that location is not license plate controlled which is otherwise not allowed.
Setting up the Products Section
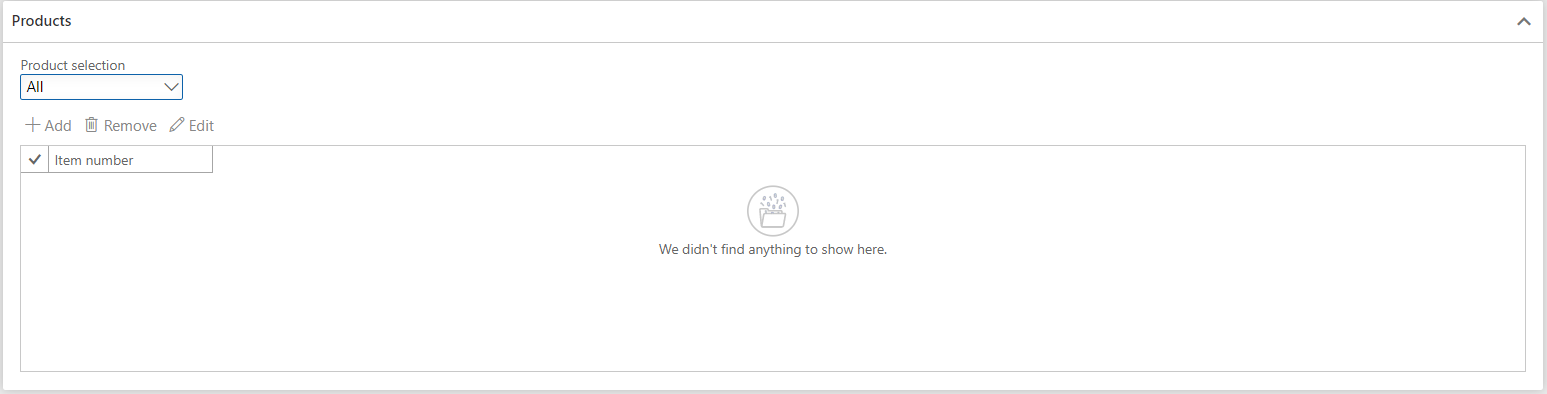
The final setup on the Work Policies is the Products section. This step allows you only to apply this setting to certain products. For our example, we are going to prevent all Raw Material Picking work from being created for our location “FL-012,” and that is accomplished by setting the Product Selection field to “All.” But if we only wanted to prevent a few items, such as subassemblies or product stored line-side, then we would need to specify each of those products in this section of the form. The setting of “Selected” would need to be used for the Product Selection field in such scenarios.
Testing the Work Policies
Once the Work Policy is created and associated with the applicable location(s), the testing can begin. For my example, the location “FL-012” will be set as the Production Input location, so I should not get any work from Releasing an applicable production order.
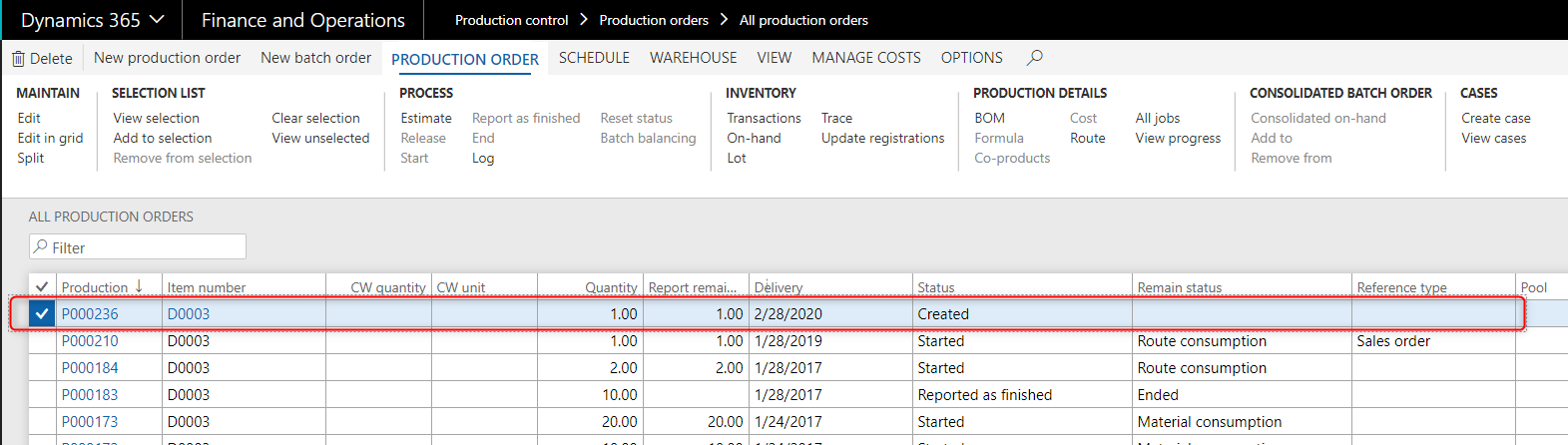
Production Order P000236 was created for the associated Warehouse, with a single item on the Bill of Materials. The only inventory for this item is in a location that is not “FL-012.”
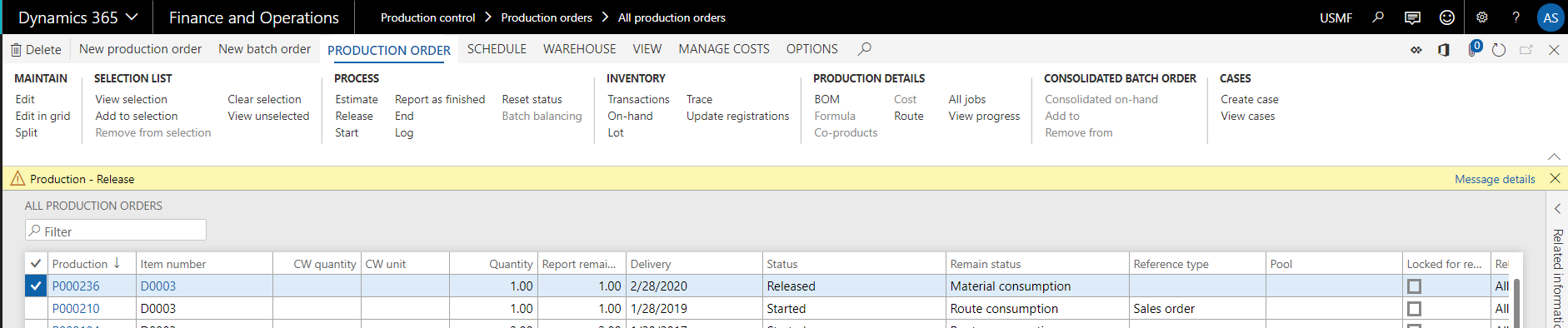
Upon Release of this production order, a notification is displayed that no Work is created. This is due to my setup of the input location but will require that I use another means to get the inventory picked to the production order.
This can be useful for the material you wish to manually assign to the production order via the Production order form, or the mobile device.
But the real functionality of this lies in the ability to ensure picking and put away work is not created for locations that are used as staging locations that are located between production processes. The stopping of Finished Goods Put Away work is likely more useful since you can also allow users to manually move inventory from certain production lines instead of directing the put-away.
Have any questions about Dynamics 365 work policies? Please contact our D365FO experts at any time!